Happy accident: Mechanical engineering researchers find better design for microsensors
Microelectromechanical systems (MEMS) are used in accelerometers, gyroscopes, pressure and vibration sensors
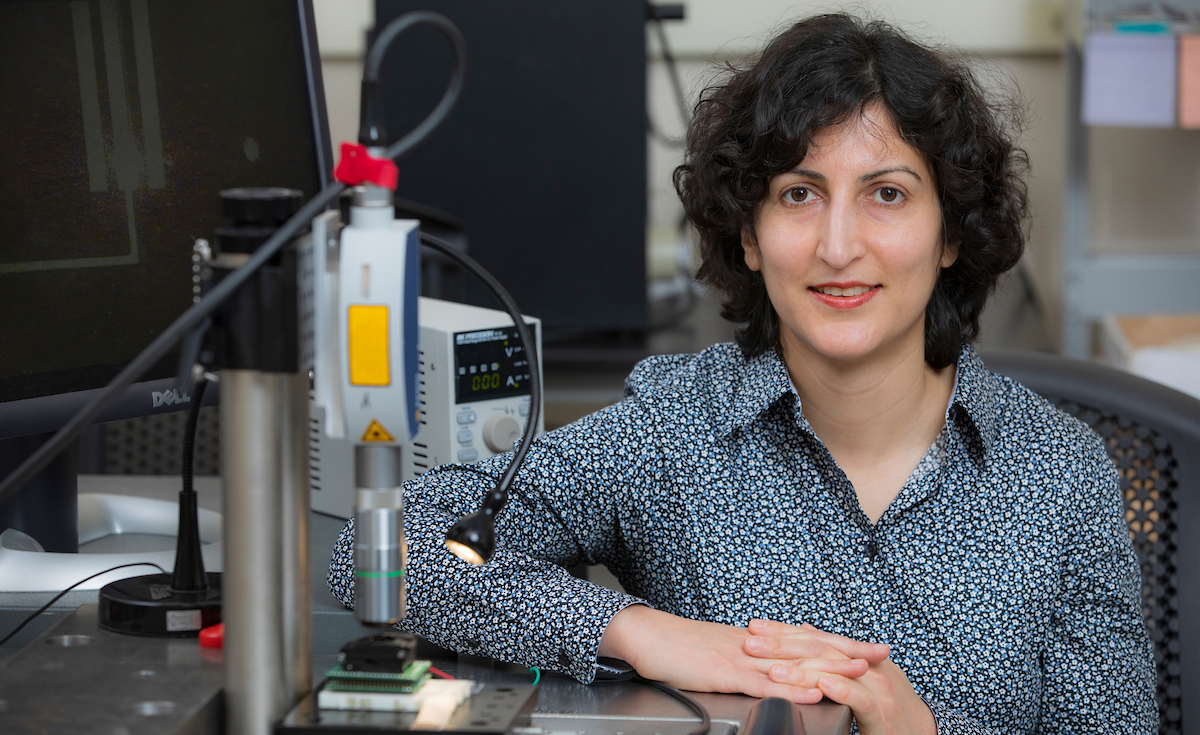
Researchers from Binghamton University and Northeastern University have found a way to improve the tiny sensors used in everything from cellphones and smart watches to biomedical devices.
A study published recently in the journal Small shows a better design for microelectromechanical systems (MEMS), which are microscopic devices with moving parts often produced in the same way that electronics are. They are used in a variety of everyday devices such as accelerometers, gyroscopes, pressure and vibration sensors.
Professor Shahrzad “Sherry” Towfighian — a faculty member in the Thomas J. Watson College of Engineering and Applied Science’s Department of Mechanical Engineering — collaborated with PhD students Mohammad Mousavi, PhD ’23, and Mohammad Alzgool, and Northeastern Assistant Professor Benyamin Davaji on the paper.
Over the past few years, Towfighian has designed devices measuring 1 millimeter square that use triboelectricty. They collect energy from friction between two microsurfaces and produce a signal when a shock is received. They have improved performance of these devices to have a better sensitivity and robustness.
For this current research, “we made a MEMS accelerometer that was initially flat with four springs on the side,” she said. “You can think of it like a suspended plate, and if you put the base on something that is moving, one will have relative motion with respect to other one. The top plate also will impact the bottom plate, and that friction converts to charges on surfaces because of contact and separation, so we have made these accelerometers self-powered.”
However, one batch of MEMS — made using advanced micro-fabrication techniques at Cornell University’s NanoScale Facility — came out wrong. Instead of the tiny surfaces being flat, they were dome-shaped and had two broken springs. Towfighian and her team nearly through them in the trash but decided to test them on the shaker at her MEMS and Energy Harvesting Laboratory.
“We realized these devices are actually more resilient,” she said. “They could resist up to 70G [70 times normal gravity on Earth] without any sign of breakage, and they gave us the largest output voltage. With a higher signal-to-noise ratio, the accelerometer is more sensitive and has better detection.”
Towfighian already has ideas about where the improved MEMS could be used, such as airbag deployment devices or extreme environments. First, however, she and her team need to develop a more controlled way of making them so that they come out in the uniform curved structures they want instead of randomly.
“We will design all later devices based on this dome shape that gives us larger range of motion and more resilience so that more robust devices can be created,” she said.
Since receiving his PhD, Mousavi is an engineer at Knowles Corp. working on state-of-the-art MEMS microphones.
Small is among the top multidisciplinary journals covering a broad spectrum of topics at the nano- and microscale at the interface of materials science, chemistry, physics, engineering, medicine and biology.