Commencement profile 2020: Ryan Cadwell
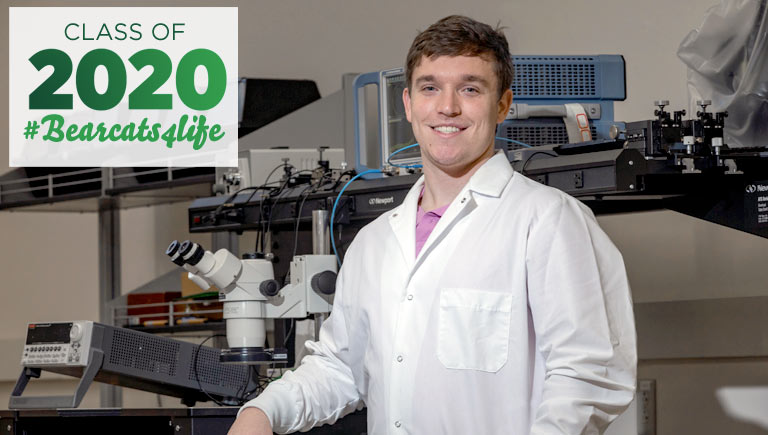
Ryan Cadwell ’18 didn’t know much about materials science when he arrived at Binghamton University as an undergraduate. He left this spring with a master’s degree and a job lined up in engineering design.
Along the way, he took an internship in Germany, co-founded the College Progressives, built a wheelchair for a cat and conducted research in the clean room at Binghamton’s Center for Advanced Microelectronics Manufacturing (CAMM).
“A lot of people say, ‘Follow your passion.’ I mean, there’s a point to that,” Cadwell said. “But for me, I’ve considered college like a financial investment. I should evaluate what the return would be. That’s partly why I chose engineering. I also thought technology was a really good way to make a large impact on the world, from a humanitarian perspective. I did do something I was interested in, but I was also concerned with making sure I can do something that’s marketable.”
Cadwell decided to go to a SUNY school after his physics teacher at Whitney Point High School told him about the New York State STEM Incentive Program, which provides tuition awards to New York residents attending college in state. He settled on studying electrical engineering at Binghamton with the idea that he could one day design solar panels or medical equipment.
As a sophomore, Cadwell took a class on semiconductors and began learning more about the intersection of engineering and materials science. He enjoyed the subject so much that he served as a course assistant for that class as a junior.
He learned about the CAMM when it appeared on a list of possible senior capstone projects. Every project was given a budget, but that one was listed with zero dollars.
“Now I know they’re not going to give us a project that has no funding,” he said. “So I was thinking that maybe that’s a blank check. Maybe this project has a lot of money and a lot of importance. And I was kind of right about that because we easily spent a few hundred dollars on that project.”
CAMM researchers create flexible electronics by printing with metals on plastics using a roll-to-roll system. The CAMM is also the New York node of NextFlex, a federal initiative to advance flexible hybrid electronics manufacturing, and home to the Center for Flexible Hybrid Medical Device Manufacturing, designated a Center for Advanced Technology by the state.
Cadwell’s senior design group, working under the direction of CAMM Director Mark Poliks, built an inspection platform for use at the CAMM that relied on lights and a microscope camera to detect scratches or dust on rolls of printed electronics.
“One of the challenges is that once you deposit the metal or the insulator, you need to inspect it to see if it’s clean enough,” Cadwell said. “And if you’re patterning wires onto these rolls, you would also want to check and see if the wires are well-formed or if one of the wires is not connected.”
The experience opened new doors for Cadwell, who decided to continue at Binghamton for a graduate degree. The decision was made easier when he received support through the National Science Foundation’s S-STEM (Scholarship in Science, Technology, Engineering and Mathematics) scholarship program.
With help from Poliks, Cadwell also lined up a three-month internship at Applied Materials in Germany the summer after he finished his undergraduate work.
As a grad student, Cadwell’s research focused on printed radio frequency (RF) electronics. “That’s basically anything wireless,” he said. “Like Wi-Fi radio or anything that you might think of with the Internet of Things or smart appliances.”
Applications could include tags on products so a retailer could have a complete inventory of everything in a store at any given moment. Printed RF sensors could also be attached to a bridge or an airplane to make it easier to monitor vibrations. Such sensors are expected to make it easier and less expensive to monitor patients’ heart rates on a continuous basis, too.
Some of Cadwell’s projects with Poliks involved creating simple radio frequency components using aerosol jet printing. The process is akin to the inkjet printers found in many home offices, though it requires far more precision, and the researchers are using silver nanoparticles rather than the kind of ink you’d get at Staples.
The group created RF components including antennae using metals printed on plastics. These flexible components’ performance was measured, with promising results.
“Once we confirm that we can make the components, then we can put the components together to make devices,” Cadwell said. “But first, we wanted to verify that the components would be able to perform well enough.”
Scott Miller, director of technology for NextFlex, said Cadwell was a critical part of the DataCube project undertaken by Binghamton University, NextFlex and other partners in collaboration with the Air Force Research Laboratory.
“Ryan’s leadership has been clear in the project from the time he joined,” Miller said. “He has demonstrated technical expertise as well as the ability to plan and organize work and collaborate with a diverse team.”
Cadwell accepted a position with a design division of Anaren/TTM just before the coronavirus pandemic began and moved to Syracuse so he could begin work in July.
Anaren makes electronic components for companies such as Lockheed Martin and Northrop Grumman. The firm’s radar and satellite communications technology has military applications; customers also include cell phone companies.
Poliks, Empire Innovation Professor of Engineering, worked in industry for decades and believes Cadwell is well prepared for the job.
“It has been a privilege to work with Ryan over the last three years,” Poliks said. “He developed expertise in radio frequency design, modeling, fabrication and testing and made significant contributions to several of our research programs.”